Role of Dental Milling Burs in Modern Dental Restorations
Role of Dental Milling Burs in Modern Dental Restorations
Blog Article
The world of dental care has experienced an innovative transformation over the last couple of years, with dental CAD/CAM (computer-aided design/computer-aided manufacturing) modern technology at the leading edge of this evolution. This high-tech advancement employs sophisticated software application and accurate equipment to style and manufacture dental remediations, such as crowns, bridges, onlays, veneers, and inlays. Dental CAD/CAM milling burs are a necessary component in this procedure, playing an essential role in forming complex dental reconstructions with amazing precision.
Milling burs are cutting devices utilized along with dental milling machines to take and finish dental prosthetics from numerous materials. These devices should be sharp and extremely long lasting, given the accuracy required and the solidity of materials they commonly work with. Normal materials include resins, porcelains, and metals, although increasingly, zirconia has come to be the material of option for many dental reconstructions due to its remarkable toughness, biocompatibility, and visual possibility.
Dental zirconia blanks, occasionally referred to as zirconia discs or blocks, are pre-manufactured kinds of zirconia used in the milling procedure. Zirconia, a crystalline form of zirconium dioxide (ZrO2), stands apart for its mechanical properties, which are similar to those of metals. These homes consist of high fracture durability, resistance to wear, and a shade that closely imitates all-natural teeth, making it perfect for dental applications. The manufacturing of dental zirconia starts with the formation of these spaces. They are fabricated under high pressure and temperature level conditions, which impart premium density and mechanical attributes.
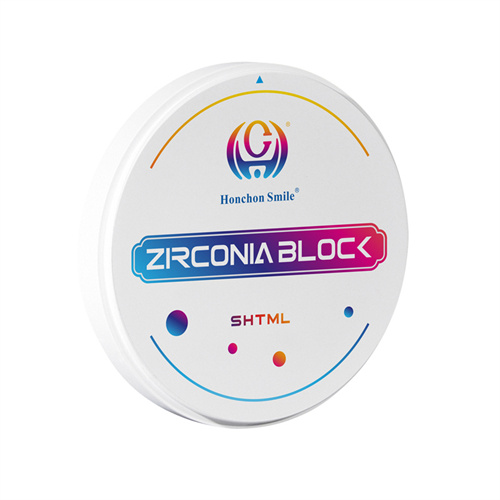
Check out the current advancements in dental CAD/CAM technology, zirconia milling, and 5-axis dental milling makers that are reinventing corrective dentistry. Discover how developments like Dental Zirconia blank are boosting accuracy, efficiency, and patient fulfillment in contemporary dental treatment.
When the zirconia blanks are created, they need to be sintered, typically in a zirconia sintering furnace. Sintering is a thermal procedure designed to develop a solid mass from powder without thawing it. During sintering, the zirconia bits fuse together at heats, enhancing the product's density and mechanical buildings while accomplishing the wanted translucency and shade slopes. A zirconia sintering furnace is a specific tool with the ability of attaining the heats required for this procedure, often in the variety of 1350 ° C to 1600 ° C. The sintering process is important, as it stabilizes the zirconia structure and secure its aesthetic and biocompatible top qualities.
Advanced milling machines, especially 5-axis dental milling equipments, have reinvented the manufacturing of dental restorations. Generally, dental reconstructions needed labor-intensive procedures and a substantial amount of time to create. The advancement to 5-axis technology has transformed this dramatically. Unlike 3-axis makers, which relocate three linear axes (Y, z, and x), 5-axis equipments add two added rotational axes (A and B). This offers the milling machine the flexibility to approach the zirconia blank from any type of angle, which is seriously important for producing complicated forms and undercuts accurately and effectively. The outcome is precision-crafted reconstructions that fit better, feel a lot more comfy, and look even more all-natural.
These innovative materials incorporate the advantages of multi-layered zirconia with the accuracy of 3D printing innovation. The multi-layered element refers to the gradient in color and translucency within the zirconia block, mimicking the all-natural change from dentin to enamel located in genuine teeth.
3D printing innovation has added another layer of customization and precision to this strategy. By incorporating CAD/CAM styles with 3D printing, the elaborate details of the dental restoration can be captured and published layer by layer. This leads to even higher precision in fit and aesthetics, which is paramount for patient satisfaction.
The mix of dental CAD/CAM systems, high-quality milling burs, dental zirconia blanks, advanced sintering furnaces, 5-axis milling devices, and the current advancement in 3D plus Multilayer Blocks exhibits the future of dental prosthetics. These technologies not just make certain precision and dependability yet also streamline the production process, making it faster and more cost-effective. The causal sequence of these improvements covers far beyond suppliers and research laboratories. Dental professionals can offer better service with quicker turn-around times, while clients profit from even more long lasting, better-fitting, and aesthetically pleasing restorations. The change from standard methods to electronic process in dental methods highlights the move in the direction of improving precision, effectiveness, and overall patient experience.
As an example, the precision afforded by these modern technologies implies prosthetics can be made and fabricated with a high level of precision, lowering the requirement for duplicated modifications or fittings. This degree of precision is mainly driven by the quality of dental CAD/CAM systems and using premium milling burs efficient in fine outlining. The processing of dental zirconia spaces in zirconia sintering furnaces makes sure that the last item meets the greatest criteria of sturdiness and biocompatibility.
The arrival of 5-axis dental milling machines has expanded the scope of what is feasible in corrective dentistry. These equipments can mill complex geometries and fine information which were not possible before, paving the means for much more innovative dental solutions. This technological jump has also made it feasible to utilize 3D plus Multilayer Blocks successfully. These multilayer blocks provide natural-looking remediations that reproduce the gradation of shade and clarity found in genuine teeth.
On top of that, the constant growth in zirconia products and CAD/CAM technologies perpetuates a more efficient and effective dental care setting. Dental experts can currently attain even more predictable end results, reducing chair time and enhancing patient fulfillment. The detailed assimilation of these technologies into routine dental technique signifies a seismic shift from reactive to positive dental treatment, where digital impacts, precise milling, and instant changes become conventional practice.
By minimizing material waste and maximizing the use of resources, dental methods can operate extra sustainably. The worldwide combination of these sophisticated materials and machines into dental educational program ensures that future dental professionals are skilled in the newest technological breakthroughs, cultivating a society of constant renovation and advancement.
In summary, the harmony between dental CAD/CAM systems, robust milling burs, high-grade zirconia blanks, reliable zirconia sintering heating systems, cutting edge 5-axis dental milling equipments, and advanced 3D plus Multilayer Blocks is driving a new age in dentistry. This combination is transforming just how dental remediations are made, produced, and executed, bring about much better end results for both patients and dental experts. As technology continues to develop, the future holds also much more pledge for advancements that will better change dental care, making it a lot more precise, effective, and patient-friendly than ever. Report this page